Products Used | Trac-Mount™ Idler |
---|---|
Product Types Used | Transfer Point Solutions , Belt Support |
Solutions | Installation , Walk The Belt™ |
Industry | Coal-Fired Power |
Customer | Sasol Synfuels, Secunda, Mpumalanga, South Africa |
Problem
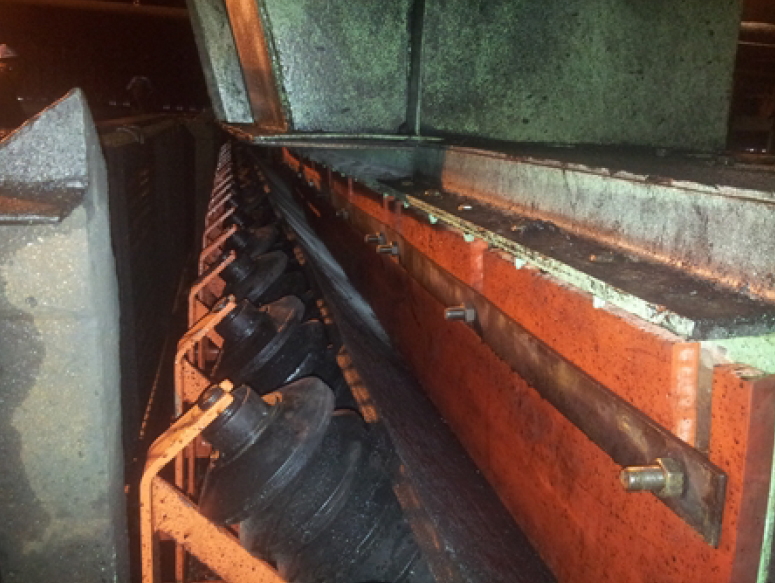
Sasol Synfuels was formed in 1950 to commercialize coal-to-liquids in South Africa, and has evolved into an international energy and chemical company that employs more than 34,000 people in 38 different countries. The coal processing plant in Secunda produces a wet coal slurry that is pressed into fuel cakes, which drop down a 5 meter chute. With belt speeds of around 3.6 meters per second, the operation processes approx. 1.6 million tons per month. The large volume of material and relatively high speed had a tendency to release small amounts of spillage, which collected into significant accumulations, requiring workers to remove the potential safety hazards and wash the material down into a specially-designed containment system.
Solution
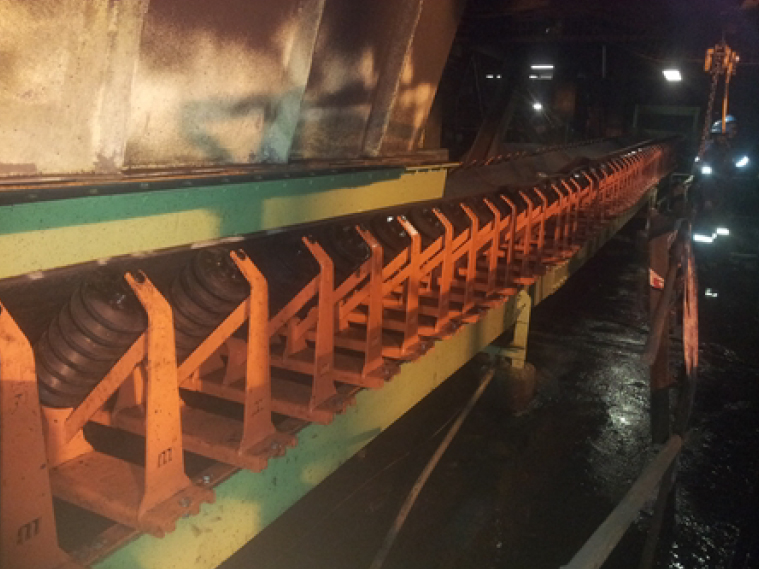
The containment system required a large amount of water and left Sasol with a significant amount of waste material that had to be addressed. They were looking for a way to prevent the spillage from escaping the process stream in the first place, so they could avoid the lost material and focus our personnel on revenue-generating activity.
Martin inspected the five belts. “We found there was a loss of stability in the belt path as it passed over certain idlers,” observed Technical Sales Rep Ronald Wilmot. “The unwanted motion was disturbing the material enough to liberate small amounts at a time from the flow. Since there was no skirt seal on these belts, the resulting spillage was uncontained.”
Martin installed a total of 138 Trac-Mount™ Idler frames on three 900 mm wide belts structures. Once the source of the spillage problem was addressed by stabilizing the belt, technicians also installed 42 meters of polyurethane skirting to provide additional dust sealing.
Results
The new components from Martin South Africa are proving effective at containing fugitive material, minimizing safety hazards and lost production time, while significantly reducing maintenance and wash water usage.
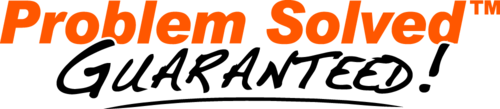
We've solved your problem somewhere before!
While your problem seems unique and frustrating, with 70+ years of solving similar problems around the world, and with the most experienced and educated people on our teams, we can assure you that we’ve “Been There, Done That.” At least close enough to know what needs to be done next and adjust for your situation.
Put Us To The Test For Free! Let Us Give You a Solution.